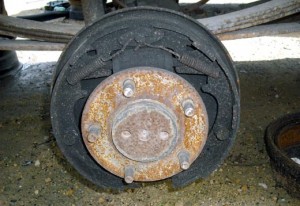
According to Bendix, brake systems are very sensitive to rust and corrosion and should receive a thorough cleaning in preparation for fresh lubricant, hardware and friction material. Residual rust or corrosion leftin critical areas can begin to cause brake issues almost immediately.
Caliper areas that are subject to movement or retain components or hardware should be cleaned, along with the pin bores. This means the calipers need to be disassembled during pad replacement. Bendix recommends using a round wire brush and cleaner to remove old lubricant and corrosion. Use a fine polishing disc in a die grinder at a lower speeds to clean the area. Avoid being too aggressive, especially with aluminum components,to ensure you only remove corrosion and not any of the metal. Be sure any areas on anti‐rattle clips or hardware are free of debris as this can affecttheir performance over the life of the brake job.
Brake pad abutments need to be clean and smooth. If there are any notches or grooves caused by pad movement, Bendix recommends these parts be replaced.Damage like this can cause excessive pad movement that leads to noise and vibration.
Hub assemblies should be cleaned with a polishing pad to clean rust from the hub face. Then use an over‐the‐stud hub cleaner to getin next to the studs. Leaving corrosion in these areas is one ofthe top causes for pulsations after a job is completed.
New or machined rotors should be washed with soap, warm water and a stiff brush to remove metal particles from the surface. If this final step isn’t taken, brake noise may likely result. It can also prevent proper filming ofthe rotor which will keep the new parts from getting their expected mileage. Bendix recommends you also clean the rear calipers and drum and parking brake systems. All these components should receive a good cleaning, inspection, lubrication and adjustment before the vehicle hits the road.
For more information and tech tips visit www.bendixbrakes.com
Comments are closed.